
AdLocal
MARKETING AGENCY
Making Connections
Delivering Results
ALL YOU NEED TO BUILD YOUR BUSINESS ONLINE
One of the Most Trusted Marketing Consulting Firms in Madison Heights, MI
Ad Local Marketing Agency is your premier destination for top-notch marketing agency services in Madison Heights, MI. We are a team of dedicated professionals specializing in providing exceptional marketing solutions to businesses in the local community. Whether you need help with digital marketing, social media management, reputation management, or SEO, we have the expertise and experience to take your brand to new heights.
Customized Marketing Solutions
As one of the leading marketing consulting firms in Madison Heights, MI, we understand the unique challenges and opportunities local businesses face. We aim to help you navigate the ever-evolving digital landscape and craft effective strategies that drive tangible results. With our tailored local online marketing solutions, we can assist you in reaching your target audience and maximizing your online presence.
Our digital marketing consultants are passionate about helping businesses succeed. They work closely with you to learn what you aim to achieve, analyzing your current marketing strategy to develop the most effective strategies to get the desired results. From website optimization to content marketing, pay-per-click advertising, to email campaigns, we employ comprehensive strategies to ensure your brand receives the visibility it deserves.

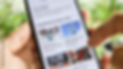
The Best Local Online Marketing
Harnessing the power of social media marketing, we can help you connect with your audience on popular platforms such as Facebook, Instagram, Twitter, and LinkedIn. Our team will develop engaging content, manage your social media accounts, and implement targeted advertising campaigns to expand your reach and engage with potential customers.
In addition to our digital marketing expertise, we also offer reputation management services to safeguard your brand's image online. We proactively monitor and address customer feedback, handle negative reviews, and implement strategies to enhance your online reputation.
Our search engine optimization (SEO) services boost your business's visibility. Our SEO specialists will optimize your website, conduct keyword research, and develop content strategies to improve your organic search rankings, driving more qualified traffic.
Our comprehensive suite of services also includes listing builder solutions to ensure your business information is accurate and consistent across online directories, helping you attract local customers. Furthermore, we offer billboard and digital advertising solutions to reach a wider audience and create brand awareness.
Are you ready to take your marketing efforts to the next level? Contact us today to schedule a consultation with our expert team in Madison Heights, MI. Let us help you unlock your business's full potential with our effective and results-driven marketing strategies.
OUR SERVICES
Our top priority is to create higher visibility for your business through branding, social media advertising, search engine optimization, bidding on specific keywords to drive traffic to your website, etc. All of our packages are fully customizable and we can flexibly work within any client’s marketing needs and budget.

Website Service
At AdLocal Marketing Agency, our talented team of experienced designers and developers work together to provide your company with a stunning custom website that is not only user- and mobile-friendly, but fast, secure, and reliable, too.
Our website designers work to ensure that your site is responsively designed, so visitors can use your website whether they are on their personal computer at home or on their phone on-the-go. Utilizing user-friendly, industry-standard design principles, our designers keep navigability and readability in mind so that the user experience flows and is intuitive rather than a hassle.
Digital Media
AdLocal is a leading provider of technology-enabled digital performance advertising solutions connecting consumers and advertisers.
AdLocal leverages the best processes and technology in the industry to provide digital performance advertising campaigns that grow business, offer visibility into the consumer experience and provide accountability for every media dollar spent.


Print Design
Whether you want to attract new customers, thank existing ones, or promote an offer, there’s nothing like high-quality print marketing to get the job done. AdLocal experts will help you create custom brochures, flyers, postcards and more. Our mailing services will help you send them out to those most likely to support your company.
OUR CLIENTS

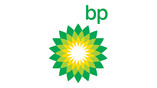
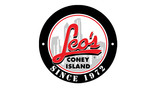
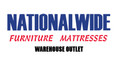



Check out our success stories to learn how AdLocal® has helped local businesses and multi-location brands find success with digital marketing.
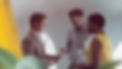
SERVICE PARTNERS



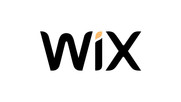
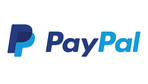



